1.引言
安慶分公司化肥一部合成氨裝置中,D1502氨分離器占有十分重要的地位。從氨合成塔出來的氨氣壓力18.OMPa,溫度326℃左右,經過兩級氨冷器降溫后,在D1502中進行液氨分離,分離出來的成品氨送尿素裝置做原料或送氨庫。其壓力為3.5MPa,溫度為-50℃左右。而D1502氨分離器上半部未合成的合成氣與合成氣壓縮機高壓缸出口的新鮮氣一道送K1502循環壓縮機進行升壓,再送到合成塔進行合成。因此,D1502液位控制系統運行的可靠性直接影響到整個合成系統的正常生產。本文在分析影響D1502液位控制系統的一些因素的基礎上,提出了相應的改進措施。
2.控制系統概述
在D1502氨分離器液位控制中,若液位過高,會引起系統超壓,嚴重時造成氣相帶液,損壞K1502循環段壓縮機。一般情況下,自動脫扣裝置將使壓縮機隔離,保護設備。若液位過低,氣相高壓易串至成品氨低壓管線,將發生事故。因此,D1502的液位監測系統必須確保靈、準、穩。
原監測系統采用兩臺液位測量變送器,信號送總控,用于液位控制與顯示。同時設有液位浮筒開關,帶[1]聯鎖,高液位時動作,合成系統停車。如圖1所示。
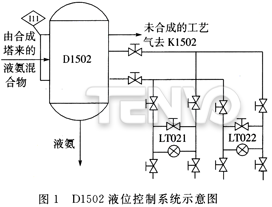
在液位調節系統中,采用兩臺Fishet 公司的DBQ型單座氣開式調節閥LV021A/B進行并聯互備,該閥具有Ⅳ級以上泄漏等級,密封可靠,動作流暢。在合成氨開車中,該閥先是關閉,使系統建立液位,隨著生產逐步正常,產量加大,閥門逐漸打開,以滿足生產,將液氨輸送至下一道工序。若LV021A調節閥出現故障,需切換到LV021B閥進行運行。此時,只能通過切換現場氣動切換開關HS021,將送到LV021A閥的氣信號切換到LV021B閥,以維持生產。
3.調節閥對控制系統的影響
3.1 現狀
LV021A/B閥在運行中經常卡死在70%左右的閥位上,無法調節,造成D1502液位上漲,引起系統超壓,[1]高液位聯鎖動作,合成系統停車。嚴重時氣相帶液,損壞K1502循環段壓縮機。或是D1502液位迅速下降,液位過低,氣相高壓串至成品氨低壓管線而發生事故。在處理閥卡過程中,考慮到該閥壓力高,壓差大,閥芯上下需要均壓,曾采用DB型閥芯結構,即對原閥芯導向部分對開兩道均壓槽,確保閥芯在運行中滿足均壓。同時,更換了備件閥籠,經過檢查測試,完全沒有效果(南京廠正常生產時該閥的開度僅在50%左右)。
3.2 理論分析
LV021A/B調節閥規格單如下表:
工藝參數 | 調節閥設備參數 | ||
介質 | NH3 | 閥門型號 | 667DBQ50 |
介質密度(Kg/m3) | 638.6 | 公稱通徑(in) | 2〃 |
操作溫度(℃) | 0 | 閥芯(in) | 3/4〃 |
最小流量(m3/h) | 6.19 | 流通能力(Cv) | 11.8 |
最大流量(m3/h) | 75.4 | 閥體等級(Lbs) | 2500#BW |
正常流量(m3/h) | 65 | 閥體材質 | Carbon Steel |
入口壓力(MPa) | 25.8 | 內件材質 | AISI 440C |
工作壓差(MPa) | 17.0 | 流量特性 | EQ% |
關閉壓差(MPa) | 26.0 | 彈簧范圍(MPa) | 0.04-0.2 |
飽和蒸汽壓(MPa) | 0.438 | 調校范圍(MPa) | 0.12-0.2 |
3.2.1阻塞流判定
(1)根據調節閥規格單,查參數:FL、PC
DBQ型閥為單座流開閥,查表得FL=0.9,PC=11.45
(2)判定流動狀態
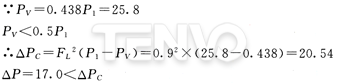
所以,該調節系統中,液態氨的流動狀態為正常流動,非阻塞流。
因此,流量系數的計算公式為:

式中:FL——壓力恢復系數;
C——調節閥的流量系數;
PC——臨界壓力(氨)(MPa);
Q——介質流量(m3/h);
PV——飽和蒸汽壓(MPa);
ρ——介質密度(103kg/m3);
P1——人口壓力(MPa);
△P——工作壓差(MPa);
△Pc——臨界壓差(MPa)。
由于C與Cν定義不同,試驗所得的數值也不同,它們之間的換算關系為:
3.2.2 開度驗算
考慮到實際生產中調節閥與管道系統的壓降分配比的影響,等百分比流量特性調節閥的開度驗算公式為:

式中:K——對應Qi的工作開度;
s——調節閥與管道系統的壓降分配比;
C——調節閥的流量系數;
△P——實際工作壓差(MPa);
Qi——某一開度下的介質流量(m3/h);
ρ——介質密度(103kg/m3)。
對于高壓系統,S一般在O.1~0.3之間選取,取S=0.2。將以上參數代人開度驗算公式計算后,得到:
在正常流量情況下,調節閥的工作開度Knom=43.5%;
在最大流量情況下,調節閥的工作開度Kmax=52.3%。
根據等百分比流量特性對數特點,該閥在理想狀態下,70%開度下的流量是50%左右流量的近兩倍,因此,可以說明實際生產中,調節閥在70%開度下的實際流通量與理論流通量不符,問題的關鍵在于控制流量特性和流量系數的閥芯上。
3.3 檢修分析
(1)表1可以看出,該閥的工藝條件對其內件的要求較高,原Fisher均選用AISI 440C硬質不銹鋼,該材質硬度較高,耐磨性、抗腐蝕能力較強,并具有良好的耐高溫性,能夠維持長期運行,在多次常規檢修中,因該閥的關閉性能要求高,每次都要對閥芯、閥座進行光刀處理,確保其密封線完好,如圖2所示,因而,導致密封線左移,這就增加了控制流量特性和流量系數的閥芯頭部的長度L1。因此,在同一開度下減少了流通量,為滿足工藝的生產要求,開度必須增大。在閥芯光刀的同時,導向部分有效長度L2相應地被加工縮短,當開度增至70%左右時,如圖3所示,閥芯導向部分的端面行至發籠導向末端,在大壓差產生的側向力作用下,導致閥芯偏磨卡死。
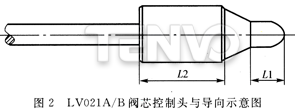
(2)就國產備件而言,由于內件材質的選用不太合理,表面硬化處理不到位,導致國產新備件更換后,很短時間即出現導向部分拉毛的痕跡,易導致卡澀。同時,國產備件閥芯、閥座密封線部位未作硬化處理(如表面堆焊司太立合金),表面硬度不高,易磨損而造成內漏,經反復光刀后,同樣易發生上述問題。
(3)在長期運行中,在大壓差產生側向力的作用下,閥芯與閥籠偏磨,造成導向間隙加大,也是影響閥卡的一個因素。
3.4 改進措施
通過上述分析,為了解決因LV021A/B閥卡的問題,而導致D1502內液氨不能及時送出,造成D1502液位上漲,引起系統超壓等安全隱患。我們采取了以下措施:
(1)利用系統中小修或計劃檢修時機,對LV021A/B閥芯頭部按相關資料加工修正到16mm左右,閥座也要作相應的光刀處理,以確保調節閥的流量特性與額定Cv值,以及良好的密封性能。
(2)將備件閥籠的導向部分延長(由原來的69.4mm延長至76mm),確保閥芯在全行程范圍內,滿負荷狀態下能有效導向運行。
減小閥芯與閥籠導向間的配合間隙,建議采用H6/g5。
(3)合理選用內件材質,推薦選用AISI 440C,內件表面必須硬化處理,其表面硬度要求達到HRC40以上,確保閥芯頭部、導向、閥籠導向及閥座密封部位的耐磨性。
(4)采取以上措施后,LV021A/B調節閥的流通能力完全能夠滿足合成系統的生產要求,未再出現因閥卡導致D1502液位控制系統故障的情況。
4.氣動切換對控制系統的影響
4.1 現狀
若LV021B調節閥故障,需及時切換到LV021A閥進行運行,此時,只能通過現場氣動切換開關HS021,將送到LV021B閥的氣信號切換到LV021A閥。而在現場進行手動切換,存在著工藝、儀表切換協調困難等嚴重問題。
(1)工藝人員首先打開LV021A閥的前后截止閥,然后,儀表人員手動切換氣動開關,同時,對LV021B進行人工排卸信號氣源,工藝人員手動關閉B閥的前后截止閥。此時若切換協調不及時,導致高液位,[1]聯鎖動作,會造成合成系統停車。
(2)儀表人員在現場手動切換氣動開關時,曾發生切換不到位,導致A/B兩臺調節閥同時不能工作,而造成合成系統停車的事故。因此,氣動開關的可靠切換必須確保。
(3)即使切換中一切順利的話,A閥由關到開,B閥由開到關,或者卡死在某個位置不動作,所導致的工況擾動,使整個系統液位波動過大,調整不及時,仍然可能導致事故。
4.2 控制系統的改進
我們充分發揮DCS的優勢,為確保LV021A/B調節閥的平穩切換,避免協調困難等不利因素,而影響工藝生產,將現場的氣動切換開關、電氣轉換器、兩臺氣動閥門定位器取消,在LV021A/B調節閥上各裝一臺電動閥門定位器,取消切換開關,在DCS中以獨立的兩套調節系統取代,這樣,在總控CRT上,工藝人員可以隨時監控LV021A/B調節閥的運行情況,如圖4。正常情況下,備用調節閥輸出閥位置零,當調節閥需要切換時,現場打開備用調節閥的前后截止閥,在CRT上操作,根據工藝生產情況在CRT上對A、B閥門開度進行調整即可,一開一關,直至原在用調節閥閥位全關,備用調節閥達到需要的開度。在切換過程中,現場液位可以在DCS上監控,從而避免了過去工藝人員在現場進行閥門切換而看不到閥位以及總控與現場協調等諸多不便,確保了安全穩定生產。
5.小結
分析了影響D1502液位控制系統中的調節閥故障和氣動切換開關切換協調兩方面的因素,提出了液位控制調節閥內件的處理措施,取消現場氣動切換開關,并以氣動改電動,在DCS上實現了LIC021A/B系統互備,在CRT上進行軟手動切換操作,極大地方便了工藝操作,提高了該系統運行的穩定性和可靠性,從而確保了D1502液位控制系統的安穩運行。
天沃-法蘭式球閥,與您資料共享!