提示:本文通過(guò)對(duì)調(diào)節(jié)閥的原理、流量特性、結(jié)構(gòu)類(lèi)型的闡述,介紹了三通調(diào)節(jié)閥在藍(lán)星0kt/a有機(jī)硅單體工程項(xiàng)目中的應(yīng)用。
1 控制閥的節(jié)流原理
從流體力學(xué)的觀(guān)點(diǎn)看,控制閥是一個(gè)局部阻力可以變化的節(jié)流元件,對(duì)不可壓縮流體,由伯努利方程可以求得通過(guò)控制閥的流體流量,如式(1):
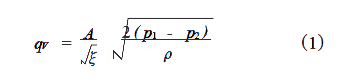
式中 qV———體積流量;
p1———閥前壓力;
p2———閥后壓力;
A———節(jié)流面積;
ξ———控制閥的阻力系數(shù);
ρ———流體的密度。
由式(1)可見(jiàn),當(dāng)A一定,p1–p2不變時(shí),qV僅隨控制閥阻力系數(shù)的變化而變化:若ξ減小,則qV增大;反之,若ξ增大,則qV減小。控制閥就是根據(jù)控制信號(hào)的大小和方向改變閥芯的行程來(lái)改變閥的阻力系數(shù),以達(dá)到調(diào)節(jié)流體流量的目的。
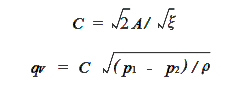
式中C———控制閥的流通能力。
C的定義:溫度為5~40℃的水,當(dāng)控制閥全開(kāi),閥兩端的壓差為0.1MPa,每小時(shí)流經(jīng)控制閥的流量數(shù)(m3/h)。控制閥流量系數(shù)將由C系列變?yōu)镵V系列。C和KV之間的關(guān)系為:KV=1.01C。
2 控制閥的流量特性
指介質(zhì)流過(guò)控制閥的相對(duì)流量與控制閥的相對(duì)開(kāi)度之間的關(guān)系,如式(2)所列。
qV/qVmax=f(l/lmax)(2)
式中qV/qVmax———相對(duì)流量,即控制閥某一開(kāi)度下的流量與全開(kāi)流量之比;
l/lmax———相對(duì)開(kāi)度,即控制閥某一開(kāi)度下的行程與全開(kāi)時(shí)行程之比。
一般來(lái)說(shuō),改變控制閥的閥芯與閥座之間的節(jié)流面積便可調(diào)節(jié)流量,但實(shí)際上由于各種因素的影響,在節(jié)流面積變化的同時(shí),還會(huì)發(fā)生閥門(mén)前后壓差的變化,而壓差的變化也會(huì)引起流量的變化。因此,流量特性有理想流量特性和工作流量特性。
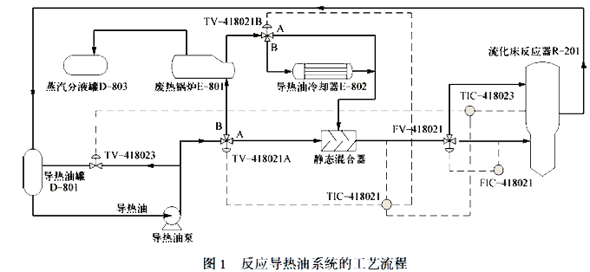
該反應(yīng)系統(tǒng)是在銅催化劑作用下,以硅粉和氯甲烷為生產(chǎn)原料,在流化床反應(yīng)器中直接合成粗甲基氯硅烷混合含塵氣體,利用一級(jí)旋風(fēng)除塵器除塵后,合成氣進(jìn)入后續(xù)系統(tǒng)中凈化分離,最終生成甲基單體。
每周期開(kāi)車(chē)前,先用導(dǎo)熱油對(duì)流化床反應(yīng)器硅粉床層升溫,來(lái)自反應(yīng)器粉料氣流輸送機(jī)的干燥粉料,以及來(lái)自氯甲烷氣體過(guò)熱器的過(guò)熱氯甲烷氣體,被導(dǎo)熱油預(yù)熱到合成反應(yīng)開(kāi)始的溫度,在銅催化劑催化條件下,使氯甲烷與硅粉進(jìn)行合成放熱反應(yīng)。放熱產(chǎn)生的熱量被導(dǎo)熱油帶出,用于產(chǎn)生中壓飽和水蒸汽。
反應(yīng)器的導(dǎo)熱油加熱結(jié)構(gòu)分兩部分,反應(yīng)器外部為半管夾套,保證外部熱量分布均勻;反應(yīng)器內(nèi)部為指型管加熱,指型管均勻分布使傳熱均勻,反應(yīng)器開(kāi)車(chē)升溫及正常反應(yīng)冷卻采用導(dǎo)熱油提供和帶走熱量,回收反應(yīng)熱用以副產(chǎn)中壓蒸汽。
開(kāi)車(chē)階段,流化床反應(yīng)器(R-201)需進(jìn)行升溫時(shí),先向反應(yīng)導(dǎo)熱油罐(D-801)注入一定量的導(dǎo)熱油,開(kāi)啟反應(yīng)導(dǎo)熱油泵,將導(dǎo)熱油送進(jìn)流化床反應(yīng)器內(nèi)部的指型循環(huán)管和外部的半管夾套,進(jìn)行流化床反應(yīng)器的床層升溫。返回D-801降溫后的導(dǎo)熱油,再次進(jìn)行循環(huán)加熱。當(dāng)流化床反應(yīng)器的床層溫度達(dá)到指定值時(shí),通入過(guò)熱氯甲烷開(kāi)始正常生產(chǎn)。正常生產(chǎn)時(shí),用導(dǎo)熱油吸收合成反應(yīng)放出的熱量。導(dǎo)熱油進(jìn)反應(yīng)器時(shí)的溫度為250℃,出反應(yīng)器時(shí)的溫度升到260℃。導(dǎo)熱油出反應(yīng)器后直接進(jìn)入反應(yīng)導(dǎo)熱油罐,與反應(yīng)導(dǎo)熱油泵旁路返回的導(dǎo)熱油混合。
反應(yīng)導(dǎo)熱油泵把加熱后的導(dǎo)熱油經(jīng)三通閥(TV-418021A),一部分送到廢熱鍋爐(E-801);另一部分進(jìn)入流化床反應(yīng)器(R-201)。兩部分的流量是由三通調(diào)節(jié)閥的閥芯同步反向調(diào)節(jié)三通閥的A、B出口的開(kāi)度來(lái)分配,這種流量調(diào)節(jié)方式無(wú)節(jié)流,流阻小,作用在閥上的壓力相對(duì)較小,不會(huì)對(duì)泵產(chǎn)生背壓,使導(dǎo)熱油泵的導(dǎo)熱油流量保持恒定。若流化床反應(yīng)器的溫度發(fā)生變化,溫度信號(hào)經(jīng)控制系統(tǒng)進(jìn)行運(yùn)算,控制三通閥的執(zhí)行機(jī)構(gòu)帶動(dòng)該閥的閥芯動(dòng)作,從而改變了三通閥的A、B口的開(kāi)度,達(dá)到調(diào)節(jié)流量的目的。假設(shè)R-201溫度偏高,TIC-418023調(diào)節(jié)器將起作用:一是加大進(jìn)入到R-201中的導(dǎo)熱油流量,以移走R-201中更多的熱量,使溫度降下來(lái)。同時(shí),TIC-418023還要改變調(diào)節(jié)器TIC-2418021的設(shè)定值,使其輸出變化,從而改變?nèi)ㄩy TV-418021A/B閥門(mén)的開(kāi)度———首先加大進(jìn)入E-801的流量,利用E-801降低進(jìn)入的導(dǎo)熱油的溫度,從而降低R-201的溫度,在E- 801中,利用被加熱的導(dǎo)熱油的熱量,生產(chǎn)1.0MPa(G)的飽和蒸汽,換熱后的導(dǎo)熱油直接進(jìn)入反應(yīng)器;如果出E-801的導(dǎo)熱油溫度偏高,即此時(shí)R- 201的溫度還繼續(xù)偏高,則利用導(dǎo)熱油冷卻器(E2802)處的三通閥(TV-418021B),將導(dǎo)熱油轉(zhuǎn)向旁路去導(dǎo)熱油冷卻器,E-802用循環(huán)冷卻水冷卻,即改變?nèi)ㄩyTV-418021B的B出口,進(jìn)入E-802的油量加大,E-802冷卻后的導(dǎo)熱油與經(jīng)TV-418021A的主流導(dǎo)熱油在靜態(tài)混合器中充分混合后去流化床反應(yīng)器,便更多地降低導(dǎo)熱油的溫度,最終能用導(dǎo)熱油移走R-201中更多熱量,使R-201的溫度回到設(shè)定值上。由三通控制閥(FV-418021)定量控制的導(dǎo)熱油進(jìn)流化床反應(yīng)器半管夾套管,余下的導(dǎo)熱油去流化床反應(yīng)器內(nèi)部指型循環(huán)管束。
在有機(jī)硅單體的生產(chǎn)過(guò)程中,反應(yīng)部分是非常關(guān)鍵的,反應(yīng)器控制得好與壞將直接影響到最終產(chǎn)品———甲基單體的產(chǎn)量和質(zhì)量。由于甲基單體合成的反應(yīng)為放熱反應(yīng),合成反應(yīng)的操作溫度需控制在300℃左右,因此及時(shí)把多余的熱量移走,才能保證反應(yīng)的順利進(jìn)行。鑒于該反應(yīng)控制的重要性和關(guān)鍵性,對(duì)反應(yīng)器的控制采用了反應(yīng)靈敏、調(diào)節(jié)速度快且控制性能穩(wěn)定,同時(shí)又不是非常復(fù)雜的串級(jí)調(diào)節(jié)系統(tǒng)。以反應(yīng)器溫度(TT-418023)作為主調(diào)參數(shù),反應(yīng)器入口的導(dǎo)熱油溫度(TT-418021)作為副調(diào)參數(shù),2臺(tái)三通控制閥(TV-418021A/B)作為副環(huán)的被調(diào)對(duì)象,當(dāng)導(dǎo)熱油流量、溫度發(fā)生變化,TT-418021 引起波動(dòng),副調(diào)節(jié)器TIC-418021)立即進(jìn)行調(diào)節(jié),通過(guò)TV-418021A/B的開(kāi)度變化,改變至廢熱鍋爐及導(dǎo)熱油冷卻器的導(dǎo)熱油量來(lái)達(dá)到不影響到反應(yīng)器溫度的目的。如果導(dǎo)熱油流量、溫度變化很大,影響到反應(yīng)器入口溫度(TT-418021)及反應(yīng)器溫度(TT-2418023)的變化,這時(shí)主調(diào)節(jié)(TIC-418023)的輸出開(kāi)始發(fā)生變化,對(duì)副調(diào)節(jié)器(TIC-418021)來(lái)說(shuō),它將接受給定值與測(cè)量值兩方面的變化,從而加速了調(diào)節(jié)過(guò)程,但此調(diào)節(jié)過(guò)程依然通過(guò)改變TV-418021A/B的開(kāi)度實(shí)現(xiàn)。除了上述通過(guò)串級(jí)控制回路來(lái)控制流化床反應(yīng)器的溫度外,還由反應(yīng)導(dǎo)熱油泵的回流流量來(lái)調(diào)節(jié),加快了調(diào)節(jié)進(jìn)程。
綜上所述,在反應(yīng)導(dǎo)熱油控制系統(tǒng)中采用了3臺(tái)三通控制閥,可以省掉3臺(tái)二通閥和3臺(tái)三通接管,既能簡(jiǎn)單、有效地進(jìn)行控制,根據(jù)反應(yīng)器所需的熱量進(jìn)行流量分配,同時(shí)又能保證半管夾套及指型管內(nèi)的流量穩(wěn)定,使整個(gè)系統(tǒng)運(yùn)行平穩(wěn),完全滿(mǎn)足工藝要求。
上海減壓閥廠(chǎng)-天沃感謝您瀏覽!