1.概述
蒸汽是一種工業領域重要的二次能源,蒸汽系統也是能源消耗的主要領域,我國產煤量的三分之一用于該系統。蒸汽疏水閥則是保障蒸汽系統正常工作、節約能源的重要自力式控制類閥門。隨著科技的發展、工業規模的不斷擴大,工業生產呈現大容量、高參數、高效低耗的趨勢,對蒸汽疏水閥節能效率要求愈來愈高的同時,對排量要求愈來愈大。如在大乙烯、大型化工裝置等工藝流程合需要排量50~160T/h的蒸汽疏水閥。目前節能型疏水閥:機械型疏水閥關鍵元件——浮球、浮筒無法滿足大口徑時介質力的要求;熱靜力型疏水閥關鍵元件——雙金屬熱動力元件單憑多組疊加;液體膨脹式單憑熱動力元件體積的增大也無法滿足大口徑時介質力的要求。
國際上超大排量先導式疏水閥技術一直被西方少數幾家大公司壟斷。國產只有仿制自由浮球+活塞的先導式疏水閥產品,沒有熱靜力+活塞主閥產品。國內在適合大排量熱靜力疏水閥的場合仍然需要選用價格高昂的進口產品或采用多組疏水閥組合的落后設計。常見的熱靜力蒸汽疏水閥主要有雙金屬型、波紋管型(液體、飽和蒸汽壓力兩種)、膜盒型和溫敏蠟型等。雙金屬熱動力元件是一種技術較為成熟的熱動力元件,主要優點在于可適用溫度高、結構簡單、安全性高、工作穩定,可用于多種介質的溫控場合。因此開發超大排量雙金屬先導可調式疏水閥,滿足國內市場以及重大成套裝備主要附件國產化對過冷或者過熱超大排量蒸汽疏水閥的需求,具有良好的應用前景、經濟效益和重大的現實意義。本文對超大排量雙金屬先導可調式疏水閥的基本原理、結構設計以及主閥導閥關鍵部件的設計進行了具體研究與探討。
2.整體結構設計
2.1 整體結構設計
超大排量雙金屬可調先導式疏水閥是將圓盤雙金屬疏水閥與大排量截止閥進行了有機的組合,采用先導式結構,通過小閥對大閥的控制,實現了對凝結水超大排量的控制;采用優化設計原理,通過活塞泄壓小孔形成氣墊、平衡彈簧等的優化組合,實現了避免關閉過快而造成高噪聲和引起管路振動甚至水擊以及有效延長密封面的壽命。
其結構主要由主閥和先導閥兩部分組成(結構簡圖如圖1所示),主閥采用的是活塞與閥芯的一體化結構,導閥采用的是圓盤雙金屬可調式結構。通過導閥帶動主閥工作,使其具有超大排量,實現排水溫度可調的功能。

2.2 基本工作原理
超大排量雙金屬可調先導式疏水閥就是以溫敏雙金屬熱動力元件組合件11作為導閥來控制主閥,當閥腔內充滿蒸汽時,雙金屬組合件處在高溫環境中而膨脹,使導閥關閉,主閥則由于介質力和彈簧力的共同作用也處于關閉狀態,從而起到了阻止蒸汽排出的作用。當閥腔內充滿的是冷空氣時,熱動力元件11則收縮使導閥打開,冷空氣就可以經由導閥、活塞15上的小孔而排出,從而起到排空氣的作用。當閥腔內流人的是冷凝水時,由于冷凝水的溫度低于雙金屬熱動力元件組合件11的動作溫度,導閥會打開排水,冷凝水通過導閥閥座孔流入主閥活塞6上腔,由于活塞的截面積遠大于主閥閥芯的截面積,活塞與主閥閥芯組件受力合力向下,則主閥打開排水。排水結束時高溫蒸汽進入導閥,導閥關閉。在活塞15上設計有泄壓緩沖小孔,主閥關閉時,活塞上腔的壓力不會迅速釋放,即主閥不會迅速關閉,從而避免了主閥閥芯與閥座的猛烈撞擊,提高了密封面的使用壽命、有效地防止了主閥關閉過速引起管路振動。
3.先導閥關鍵技術研究與設計
3.1 雙金屬組件熱動力元件受力分析
3.1.1 建立熱推力F與撓度f的數學模型形公式也可用于一般非純彎曲)。則如圖2所示雙金屬片產生了一定的彎曲變形,設中心處垂直方向上的變形量f與任一點x處的彎矩與撓度的關系為:
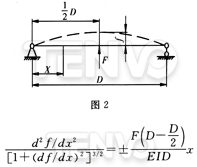
式中:D——雙金屬片外徑,m;
d——雙金屬片內徑,m;
E——雙金屬片的彈性模量,Pa;
I——雙金屬片截面的極慣性矩,m4;
F——一片雙金屬片產生的熱推力,N;
f——雙金屬片中心處垂直方向上的變形量,m;
x——雙金屬片上任一點到其邊緣的距離,m。
由于df/dx的值遠小于1,略去后積分并令x=D/2得:

對于導閥中圖3所示的環形雙金屬片,有:
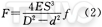
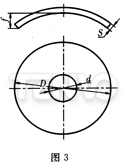
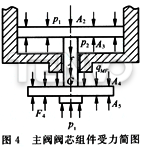
3.1.2計算熱推力
由比彎曲關系式:
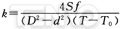
將上式代人式(2)中得:
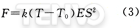
則一組金屬片產生的熱推力為:

除去凝結水作用在金屬片上的壓力后的熱推力為:

則n組金屬片的熱推力為:

式中:Po——進口壓力,Pa;
k——比彎曲,℃-1;
T——雙金屬片變形后的溫度,℃;
T0——雙金屬片開始變形時的溫度,℃;
n——雙金屬片組的個數。
3.1.3雙金屬片導閥所需動作平衡力
閉閥后,導閥內部力的平衡方程式如下:
F1≥F2-F3

式中:F2——導閥關閉后其閥孔前的力,N;
F3——導閥關閉后其閥孔后的力,N;
P1——活塞上腔介質壓力,Pa;
A1——導閥閥座孔截面積,m2。
3.1.4密封比壓q的選擇
密封比壓的計算:
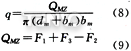
密封面的實際比壓值q應滿足下列關系:

式中:q——密封比壓,Pa;
QMZ——導閥閥座密封面上的總作用力,N;
qMB——導閥密封面上的必須比壓,Pa;
dm——導閥閥座密封面內徑,m;
bm——導閥閥座密封面寬度,m;
[q]——許用密封比壓,Pa。
3.1.5 雙金屬片組片數n的確定
聯立式(7)、(8)、(9)和(10),得
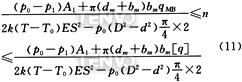
3.2先導閥口徑的設計計算
雙金屬組件熱動力元件作為超大排量疏水閥導閥的關鍵部件,其啟閉速度決定著整臺疏水閥的動作靈敏度。其靈敏度過高容易引起管路水擊現象,從而引起管路異常振動甚至導致破壞;而其靈敏度過低則將增大疏水閥的漏汽率。可見,有效地控制雙金屬組件熱動力元件的靈敏度,對疏水閥性能的穩定與提高具有重要的意義。為避免水擊現象的發生,需要對先導閥的口徑進行限制,以便控制主閥的開閥時間。
假設將先導閥安裝在長為L的管路中,流體在管路中的流速為V。(過熱蒸汽一般為40~60m/s),忽略活塞小孔的排液量可得:
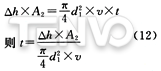
式中:△h——活塞行程,m;
A2——活塞頂部橫截面積,m2;
d1——導閥直徑,m;
Vs——管路中的流速,m/s;
ν——導閥閥座中冷凝水的流速,m/s;
t——主閥關閉時間,s。
根據水擊原理當t》2L/Vs時不會引起水擊,由以上分析可以得出導閥口徑d1,滿足
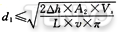
時不會發生水擊。
4.主閥關鍵技術研究
4.1 主凋閥芯組件的受力分析
根據設計工況、主閥閥座和閥瓣密封副所需要的密封比壓,對主閥閥芯組件進行受力分析可得(如圖4所示):
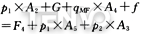
則活塞的頂部橫截面積計算式為:

其中主閥密封面上的必需比壓為:
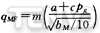
式中:G——主閥閥芯組件自身重力,N;
f——活塞環與氣缸的摩擦力,N;
qMF——主閥密封比壓力,106Pa;
A3——活塞底部橫截面積(活塞的頂部橫截面積減去閥桿的面積),m2;
A4——主閥密封面面積,10-6m2;
P2——活塞下部介質壓力,Pa;
F4——主閥彈簧回復力,N;
A5——主閥介質作用面積,m2;
m——與流體性質有關的系數;
α,c——與密封面材料有關的系數;
pg——公稱壓力,106Pa;
bM——密封面寬度,10-3m。
由以上計算式,可根據設計工況通過反復計算來優化回復彈簧的受力,進而優化主閥閥芯組件的整體結構設計。
4.2 主閥回復彈簧的設計
主閥回復彈簧力的大小直接影響到疏水閥主閥的性能,力太大容易引起水擊現象,力太小則會導致漏汽率增加,因此,對回復彈簧的設計相當必要。由4.1中的分析可知,主閥回復彈簧受到的力的大小為F4,另外,根據具體使用場合選定彈簧的材料,查表可得材料的許用應力[τ],然后按強度和剛度要求設計圓柱螺旋壓縮彈簧。
首先,在彈簧的旋繞比C=4~8范圍內初選,并由下式可得彈簧材料直徑d2為:
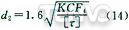
式中:K——曲度系數。
根據計算值查得d2的系列值,再由彈簧中徑D2=cd確定下D2。
彈簧的有效圈數可由下式計算:

式中:G2——彈簧材料的切變模量,109Pa;
f2:——彈簧變形量,10-3m;
k——彈簧剛度,103N/m;
kd——彈簧單圈剛度,103N/m。
由于C的不確定,可以根據不同的C值進行多組計算,比較計算結果,選取最佳方案,以便優化彈簧的受力。
4.3 主閥關閉時設計計算
主閥的關閥時間是反映整臺疏水閥性能的重要指標之一,它與整臺疏水閥的設計排量、漏汽率有著直接的關系。超大排量雙金屬可調先導式疏水閥主閥的關閥時間的長短與活塞上腔的體積、介質壓力以及活塞小孔的大小有關,根據流體力學上的原理計算如下:
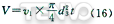
由伯努利方程可得:
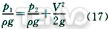
將式(16)代入式(17)可得:
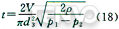
式中:V——活塞上腔體積,m3;
ν1——活塞小孔處液體流速,m/s;
d3——活塞小孔直徑,m;
ρ——液體密度,Kg/m3;
t——關閥時間,s。
由式(18)即可確定主閥的關閥時間,結合水擊原理,該時間應在滿足t》2L/Vs的同時,還要保證整臺疏水閥的漏氣率滿足要求。
5.結語
雙金屬可調先導超大排量蒸汽疏水閥是一類用于特殊場合的高參數蒸汽疏水閥,它采用的是熱靜力導閥+活塞主閥的設計,可用于有過冷度和過熱蒸汽的場合,該產品的開發可為相關應用行業提高能源利用率、節約能源開支提供了保障。
目前國內主要存在問題在于:高溫工況下國產雙金屬材料、彈簧材料性能的穩定性差,不能滿足高于250℃的使用要求,與德、美、日等發達國家有很大距離。這就要求我們聯合材料研究機構和生產企業,研發新材料,滿足需求。
綜合上述,該設計具有超大排量,可滿足工業需求,節約能源。其研發思路還可為疏水閥、減壓閥等自力式控制類閥門新產品的研發提供了一定參考。
蝶閥廠家-天沃,與您資料共享!